Introduction
A toothbrush is an essential tool in maintaining oral hygiene and overall health. Its design and manufacturing process have evolved over the years, incorporating advanced materials and technologies, well, in this article, we will delve into the intricate journey of producing a toothbrush, from the initial design stages to the final manufacturing process.
Design and Development
The process of producing a toothbrush begins with careful design and development. Designers consider factors such as ergonomics, bristle types, handle materials, and overall aesthetics. The goal is to create a toothbrush that is not only effective in cleaning teeth but also comfortable to hold and visually appealing.
1. Bristle Selection:
Toothbrush bristles come in various materials and firmness levels. Soft, medium, and hard bristles cater to different oral care needs and sensitivities. And Nylon bristles are commonly used due to their durability and flexibility.
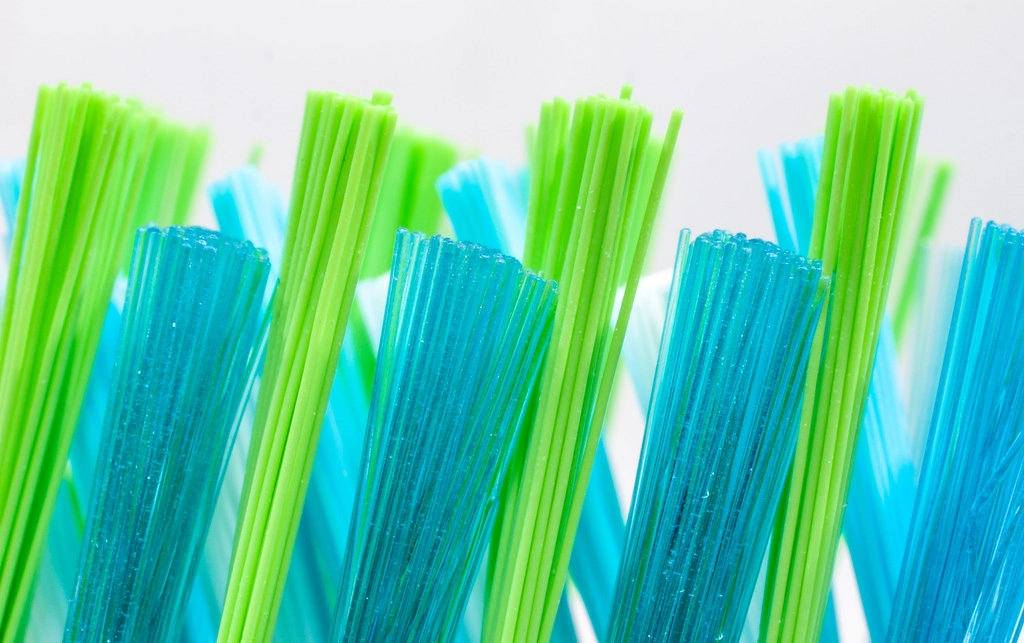
2. Handle Design:
Designers often use computer-aided design (CAD) software to create ergonomic handles that fit comfortably in the hand and provide precise control during brushing.
3. Material Choice:
Handles can be made from various materials such as plastic, rubber, or even bamboo for eco-friendly options. Each material brings unique properties to the toothbrush, influencing factors like weight, texture, and environmental impact.
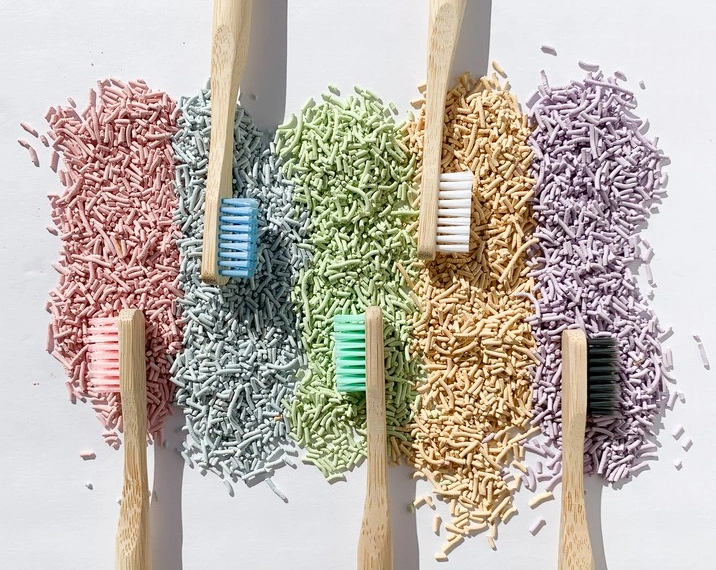
4. Incorporating Technology:
Some toothbrushes now come with technology features like vibrating bristles or timers to encourage proper brushing duration. These features are integrated during the design phase to ensure seamless functionality.
Materials and Manufacturing
Once the toothbrush design is finalized, the manufacturing process begins. This involves selecting suitable materials, setting up production lines, and adhering to quality standards.
1. Material Procurement:
The selected materials, including bristles and handle components, are sourced from suppliers. Quality control is crucial to ensure that the materials meet the required standards for safety and performance.
2. Injection Molding:
Injection molding is a widely manufacturing process for toothbrush handles. It’s also the first step in making brush handles. After Plastic pellets heated until they melt, then injected into a mold cavity. Once cooled and solidified, the mold opened to release the toothbrush handle.
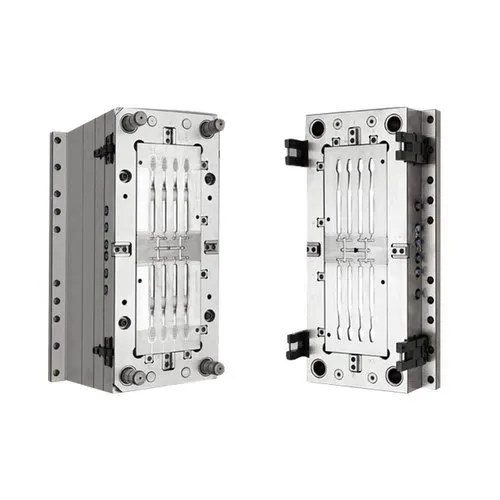
3. Bristle Planting:
Bristles anchored into the toothbrush head holes using various methods, including staple technology and anchorless tufting. These methods secure the bristles in place and ensure they remain intact during use.

4. Assembling Components:
If the toothbrush includes additional components like rubber grips or technology modules, these assembled onto the handle during this stage of production.
5. Quality Control:
Rigorous quality control checks conducted throughout the manufacturing process. Including qualified injection molding of the brush handle, inspection of the neatness of the brush bristles, and inspection of the firmness of the bristles. These checks ensure that each toothbrush meets safety and performance standards before it moves to packaging.
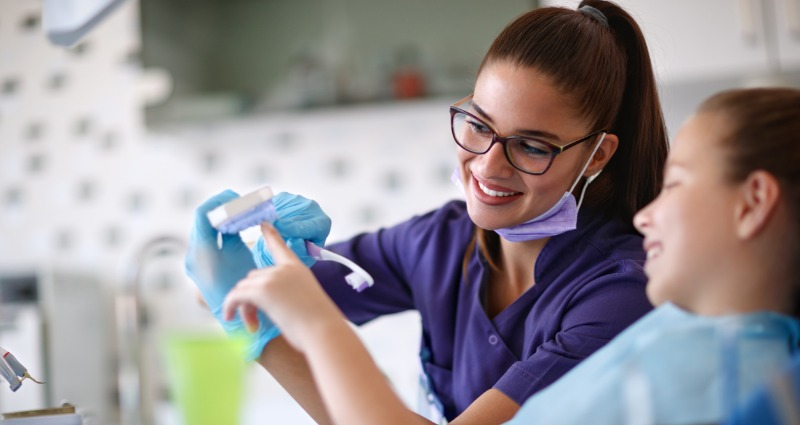
Packaging and Distribution
Packaging plays a vital role in preserving the toothbrush’s integrity and providing relevant information to the consumer. And distribution networks then ensure that the toothbrush reaches its intended market.
1. Packaging Design:
The packaging designed to not only protect the toothbrush but also to attract consumers’ attention. Clear information about the toothbrush’s features, benefits, and usage instructions is provided on the packaging.
2. Environmental Considerations:
As environmental awareness grows, manufacturers are adopting eco-friendly packaging options, reducing plastic use, and promoting recycling.
3. Distribution and Marketing:
Toothbrushes are distributed through various channels, including retail stores, online platforms, and dental offices. Marketing efforts educate consumers about the toothbrush’s unique features and benefits, helping them make informed choices.
Future Trends and Innovations
The toothbrush industry continues to evolve, embracing technological advancements and sustainable practices.
1. Smart Toothbrushes:
With the integration of sensors and connectivity, smart toothbrushes can provide real-time feedback on brushing technique and duration, enhancing oral care routines.
2. Biodegradable Materials:
Innovations in biodegradable materials offer a sustainable alternative to traditional plastic toothbrushes, addressing the growing concern of plastic waste.
3. 3D Printing:
3D printing technology allows for customized toothbrush designs and rapid prototyping, enabling greater personalization and creativity in toothbrush production.
MARBON GROUP oem production
As a professional manufacturer of toothbrush and oral irrigator / water flosser, MARBON GROUP provides various types of manual toothbrush, electric toothbrush wholesale and OEM customized services at factory price. We can provide you highly competitive prices and look forward to working with you.

Conclusion
Producing a toothbrush involves a meticulous journey from design and development to manufacturing and distribution. The marriage of innovation and traditional practices ensures that toothbrushes continue to evolve, meeting the ever-changing needs of consumers. As technology and sustainability take center stage, the toothbrush industry is poised for exciting advancements that will redefine oral hygiene for generations to come.
